Guyson blast cabinets clean extrusion and injection screws
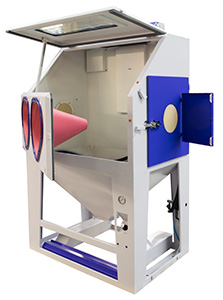
Manufacturers of plastic extruded product and compounding companies looking to clean case hardened steel extrusion screws used in their manufacturing processes can call on leading industrial finishing equipment manufacturer Guyson International for an effective solution to their cleaning problems. Guyson offers a variety of tailored blast cabinets designed especially to accommodate long extrusion and injection screws and which deliver a highly effective cleaning process, but crucially, without damaging the critical screw threads.
Based around their standard Euroblast® cabinet shells, these blast cabinets can be produced either with matching side-mounted cut-outs to the cabinet side walls, thus allowing extremely long extrusion screws to pass through the cabinet and be bead blasted clean, or alternatively with an extension box positioned on the either side of the blast chamber to accommodate long steel screws, both of these design options avoiding having to build a ‘special’ extra wide cabinet with all the higher costs that would incur for the customer.
If the cabinet with cut-outs is chosen as the preferred option, then a selection of interchangeable metal templates are provided with the machine, with appropriately sized cut-outs fitted with rubber gators and matching internal baffles for sealing to prevent media escaping, thus allowing it to accommodate extremely long extrusion screws which can pass completely through the cabinet and be bead blasted clean along their entire length.
The side extension box option can be fitted to any of the Euroblast® cabinets but is widely offered with the Euroblast 7PF as this tends to offer the best width to price ratio, being already a wide, rectangular cabinet chamber.
For this application of extrusion and injection screw bead blast cleaning, Guyson generally recommends the Euroblast PF (pressure fed) system since this is designed for speed, giving faster cleaning times (up to four times faster than suction fed venturi systems), ideal for meeting higher production requirements. Pressure feed blast systems are excellent for removing tough, hard scale and carbon deposits especially within hard-to-reach recessed areas and complex shapes and particularly those found on the extremely long extrusion screws used in twin screw compounding machines where a central core shaft is fitted with a variety of mixing, kneading, cutting and conveying elements and where removal of the black carbon deposits is especially critical in order to prevent contamination prior to any formulation of neutral colour or medical grade compounding materials.
The blast media used in this application is a specialist plastic blast media sold by Guyson. It is aggressive enough to remove the residues and carbon build-up but without causing any damage to the precision screw threads.
The plastic blast media is propelled at the encrusted screw threads by a high impact stream of air generated from a Guyson G27 (27 litre) pressure pot and directed at the threads through a tungsten blast nozzle. Completing a standard blast system set up for this application would be a cyclone separator and dust collector. The cyclone separator maintains a consistent media size within the media stream in order to achieve consistent roughness levels. The Guyson 75/16 cyclone separator creates a vortex of air that carries the heavier re-usable particles to the outside of the rotating air stream. These collect in a storage hopper ready to be re-used, whilst the lighter remaining dust, fines and undersize media are separated and collected in a Guyson C400 cartridge dust collector for disposal.
For further information about the range of Guyson blast cabinets available or to undertake free component trials on your extrusion and injection screws please contact Guyson’s Customer Service Department on 01756 799911.
About Guyson
Guyson International Limited is a privately owned family company with a world-wide reputation for excellence in the design and manufacture of blast finishing, spray wash and ultrasonic cleaning equipment. Formed over 75 years ago, the company is registered to BS EN ISO 9001: 2008 and BS OHSAS 18001:2007 and its head office is located at Skipton, North Yorkshire, in the north of England. Guyson has four international subsidiary companies: Guyson Corporation of the USA, located in Saratoga Springs, New York State; Guyson SA, situated near Paris, France; Guyson Sdn Bhd in Penang, Malaysia; and Guyson CN, in Wuxi, Jiangsu Province, China.