Guyson equipment for medical 3D printing start-up
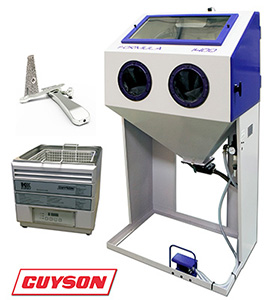
Industrial finishing equipment manufacturer Guyson International has recently installed into Fusion Implants, a new hi-tech medical start-up enterprise, one of their Formula 1400 blast cabinets, together with a 'Kerry' branded MKC14 ultrasonic bath for surface finishing and ultrasonically cleaning their 3D printed parts which are used during veterinary implant procedures. Fusion Implants takes full advantage of all the new creative design and production opportunities brought about by additive manufacturing – now being able to create components that would, in the past, have been impossible to manufacture without this new technology.
The modified Guyson Formula 1400 blast cabinet has been installed to provide the desired cosmetic finish to a range of ‘dynamic tension plates’, created from CP Grade 1 Titanium powder which is fused together using “Selective Laser Melting” (SLM) technology. The Fusion TTA implant consists of a honeycombed wedge and dynamic tension plate, both of which are fixed into position using an Ellis pin and titanium screw and used to repair cranial cruciate ligament (CCL) damage in dogs. Dr Dan Jones, General Manager of Fusion Implants said: "We needed the dynamic tension plates to have a uniform and aesthetic appearance as do the rest of the conventionally manufactured stainless steel instrumentation kit and glass bead blasting was the best process to achieve this”.
Because the components are destined for medical use, the modified Formula blast cabinet features a polyurethane bodied Guyson model 900 blast gun fitted with stainless steel airjets, a stainless steel cabinet floor, stainless steel hose coupling and a stainless steel media pick-up tube. This specification ensures that no ferrous contamination can enter the media flow whilst blasting the dynamic tension plate with Guyson’s inert Honite glass bead blast media.
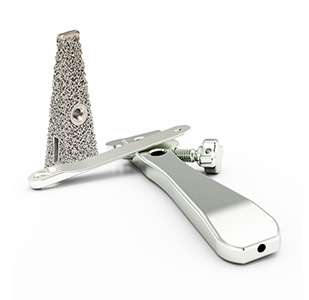
Photo Right: Fusion TTA implant wedge and dynamic tension plate - photo courtesy of Fusion Implants
The Guyson Formula blast cabinet range comprises three strong and durable steel cabinets, all ideal for light industrial applications or when blasting is required on an intermittent basis. As standard they use the industrial quality model 400 blast gun, which can be tailored to suit air supplies of between 8 and 16 CFM when blasting at 80 PSI.
The F1400 has a full height side opening door on the right hand side of the cabinet and has internal cabinet dimensions of W 815mm x D 560mm x H 591mm; large enough to accommodate most 3D prototypes. Blasting is controlled by foot pedal, thus leaving both hands free to manipulate parts under the blast nozzle when the nozzle is positioned in the gun holder or leaving one hand free to hold the gun and the other to rotate the part. The F21 dust collector comes standard with this cabinet. All Formula blast cabinets have sealed gauntlet gloves, a protected toughened glass viewing window and a quick release media changeover facility; useful if a variety of different blast media is used.
After the glass bead blasting, both components - implant wedge and dynamic tension plate - are then immersed in the Kerry MKC14 ultrasonic bath for initial cleaning and to remove any loose and residual, partially adhered titanium powder created during the ‘Selective Laser Melting’ (SLM) additive manufacturing process, or any remaining glass bead dust particles. The 3D printed medical implants are then transferred to a multi-stage cleaning and passivation line and autoclave before final packaging.
All Guyson’s microprocessor-controlled MKC baths (6, 14 and 22 litres approx.) allow the user to pre-set exact cleaning times and temperatures, ensuring the same high level of cleanliness every time. Digital control allows solution heating to be set from 20°C to 80°C in 1°C increments, so that the optimum temperature can be selected for a particular combination of component material, cleaning solution and contaminant. Process times from 6 seconds to 99.9 minutes can also be pre-programmed in 6 second increments.
All functions are controlled by a simple four-button membrane keypad. An LCD panel displays the temperature and time set by the user, the actual solution temperature and the time elapsed since the start of the cleaning process. LEDs show the status of the power supply, heater and ultrasonics.
For further information about the range of Guyson finishing products available or to undertake free component trials on your additive manufactured or 3D printed prototypes please contact Guyson’s Customer Service Department on 01756 799911.