Kerry Microsolve for cleaning switchgear electrical contacts
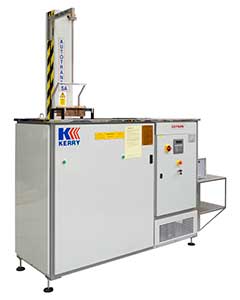
Leading industrial finishing equipment manufacturer Guyson International has recently manufactured and installed a Kerry Microsolve 350 Mono-solvent cleaning system, for cleaning electrical contacts used in switchgear, into the Staffordshire site of Mors Smitt a world leader in railway relay technology.
After the initial enquiry Mors Smitt undertook extensive sample evaluation, at Guyson’s test and development centre, including processing the bronze and carbon silver contacts with and without ultrasonics to prove the exact process needed and choose the correct machine and solvent combination. Once the cleanliness trial had been undertaken and results returned, the machine decided upon was a Kerry Microsolve 350 Mono-solvent cleaning systems with a specially designed component tray handling system to accommodate existing component handling trays. This allowed the customer to continue using hundreds of existing specially designed component trays that are used for other processes throughout their factory.
The Kerry Microsolve Mono-Solvent system manufactured by Guyson has three process stages comprising of ultrasonic cleaning, followed by vapour rinsing and freeboard drying.
Cleaning with or without the use of ultrasonics is carried out in the stage one tank by immersion of the components into the solvent. The ultrasonic transducers are mounted on the tank base and powered by the Guyson Primewave dual frequency generator incorporating ultrasonic output power control, pulsed operation of the ultrasonics (if required) and frequency modulation and sideband sweep. Stage one is also supplied with solution heating and a pumped closed-loop filtration system comprising a course strainer, fine filter cartridge, welded pipework and “O” ring sealed valves.
The second tank (stage two), is electrically heated with unique pulsed control operation allowing the solvent to boil efficiently whilst helping to minimise solvent emissions. The resulting vapour rinses the components, which are then dried in the freeboard zone (stage three). Distilled solvent, condensed by the primary cooling coils, passes through a water separator with in-line heat exchanger and returns to the ultrasonic tank, displacing contaminated solvent into the boiling sump. Distillation, together with filtration of the solvent, ensures that the ultrasonic tank is maintained at a controlled level of cleanliness.
The Guysonic generator and Primewave dual-frequency controller enables sensitive or intricately shaped parts to be effectively cleaned at frequencies of 36, 66, and 146 kHz for either single or dual frequency operation.
Low, predictable running costs
The Microsolve has proven unique solvent retention features that provide economic benefits as well as effective use of HFE (hydrofluoroether) solvents. Microsolve owners enjoy low, predictable running costs thanks to intelligent machine design - a highly effective triple coil reflux cooling system, vapour break and a 150% freeboard zone all help to minimise the loss of expensive solvent. An optional automatic solvent top-up system logs the rate of solvent usage provides factual information regarding the total consumption.
The machine is also equipped with Autotrans SA (single axis) lift which ensures consistent, repeatable delivery and extraction of the components into and out of the cleaning solution whilst also contributing to cost reductions by controlling the speed of basket movement through the vapour zone, thus reducing solvent drag-out caused by disturbance of the vapour blanket.
Cleaning trials
Prospective users of Guyson ultrasonic cleaning equipment are encouraged to submit sample components for free feasibility testing in the company’s extensive development workshop at Skipton, England. To contact Guyson International, please call +44 (0)1756 799911 or email info@guysonfr.co.uk.